New Equipment Sales: +254-701-373789
Videojet has the ink development capabilities and experience to find the right solution for your part marking needs
Our experienced team of CIJ ink chemists are experts in creating inks that work for your application, production environment, and durability requirements. They actively monitor material trends and coding requirements to ensure our ink solutions are ready to address the emerging needs of our customers.
Our development processes don’t end in the ink laboratory. Our ink development activities include customer field trials. In fact, we encourage customers to participate in our testing phases to verify the required ink performance in the targeted application. This well-established approach routinely results in overcoming the toughest printing and coding challenges.
With a portfolio of over 340 different inks, Videojet is the right partner to support you in finding the ideal ink for your application.
Adhesion and legibility Manufacturers generally understand that the material being coded influences ink performance. And while some materials, like paper, typically work well with most ink types, the plastics, rubbers, metals, and composites used to make aerospace and automotive parts can be more difficult. Did you know, for example, that new high-performance plastics using specialised plasticisers can present complex challenges to ink code adhesion?
Moreover, environmental variables like moisture, temperature, and humidity can all impact initial ink code adhesion and durability. This is especially critical in an industry where codes are expected to remain legible for years, and where parts may come into contact with solvents like fuel and lubricants. Drying and curing times afforded manufacturing processes must be accommodated as well, especially to ensure codes are durable and abrasion-resistant for the lifespan of the part.
Additionally, the time between printing the code and its first contact with a material handling component, like a belt or mechanical guide, or another product, may influence the code’s adhesion and legibility. These manufacturing process conditions can result in problems such as ink transfer or code smudging, and therefore should be considered when selecting the best ink.
Understanding the many varying factors, there are a few questions that you should ask in preparation for discussing ink selection with experts:
- What material (e.g. ABS, PE, PEX, PP, PVC, Al, Mg, Ni, steel, Ti, Zn, alloys, composites, fibreglass, glass, nylon, rubber, etc.) am I coding onto?
- Are there any surface coatings or contaminants from the manufacturing process present on the product either before or after coding?
- What product surface colour variation exists, and what is your or your customer’s requirement for visual or machine-readable code contrast?
- What is the manufacturing environment and what temperature extremes will the printer and product experience and the code need to endure?
- When and what components come into contact with the code after printing that may impact ink dry time?
- What is the operating environment for this product, and what added ink attributes are needed (e.g. heat and oil-resistance, abrasion resistance)?
Knowing the answers to the above questions will help to quickly narrow down ink selection to a handful of suitable options. Automotive and aerospace manufacturers will be well-served to partner with a coding and marking supplier that can guide their ink selection. Videojet is here to help you determine the best coding solution for your application.
Inks gallery
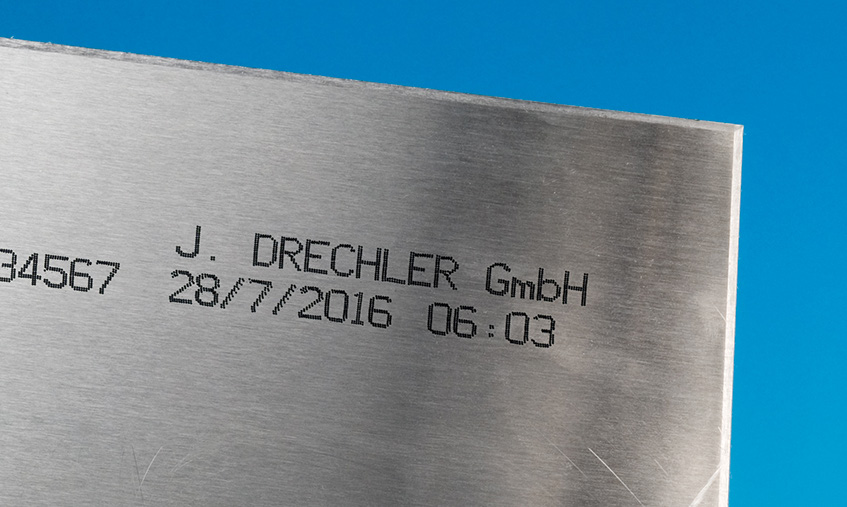
Oil penetrating
Metal parts sometimes contain lubricants that aid in their forming, bending or machining processes. Along with these lubricants, oils used as rust-preventatives can inhibit ink adhesion unless special ink chemistry is employed. Unique ink solvents and resins in Videojet’s oil penetrating inks help the inks to achieve excellent adherence through these protective layers.
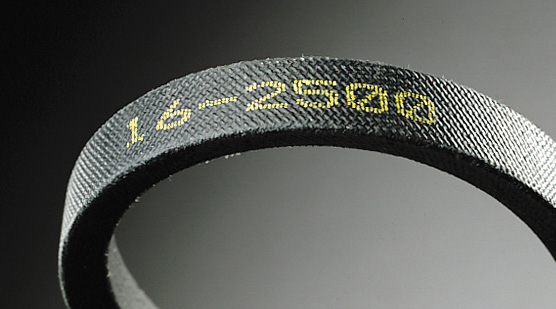
High contrast
Opaque pigmented inks are formulated to create highly visible codes, typically on dark coloured surfaces. They also resist the pressure and heat of product-to-product contact during processing. With a range of colours available, some are uniquely designed to create high visual contrast on both light and dark coloured surfaces.
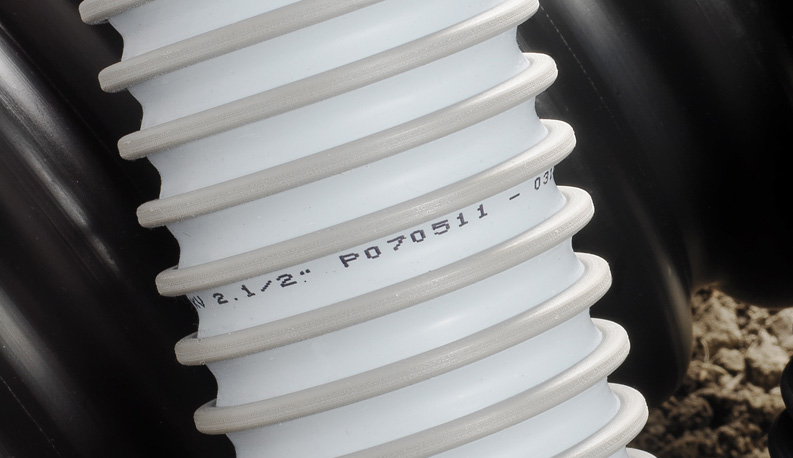
Heat / steam cure
Heat and steam-cure inks can be an ideal solution for printing on extruded plastic and rubber products where high temperatures and pressurised steam can create ink adhesion challenges. Other inks can fade or disappear during these processes while Videojet’s heat/ steam-cure inks provide good colour retention and adhesion throughout the curing process and the life of the product.

Non-transfer/high temperature-resistant
Videojet non-transfer/high temperature resistant inks are designed to minimise code offset and transfer. This can be especially important for products that are warm when coded, such as extrusions, or products where codes may have direct contact with other products or materials during storage or use. Ink code adhesion can be a challenge in these scenarios, but specialised inks can help maintain code integrity.

Pigmented black opaque
Pigmented, opaque black inks are an ideal solution for applications which require fade resistance, lightfastness, and bold black colouration. These attributes are particularly well suited to many aerospace applications, and are listed within part marking specifications for many suppliers and manufacturers within the aerospace industry.

Invisible fluorescing UV readable
Certain automotive and aerospace products may require discrete fluorescing codes and brand information that are only visible under UV lighting, either for machine or human readability. Invisible fluorescing inks are available in a range of colours and can provide an unobtrusive solution for coding and tracking products though the supply chain.
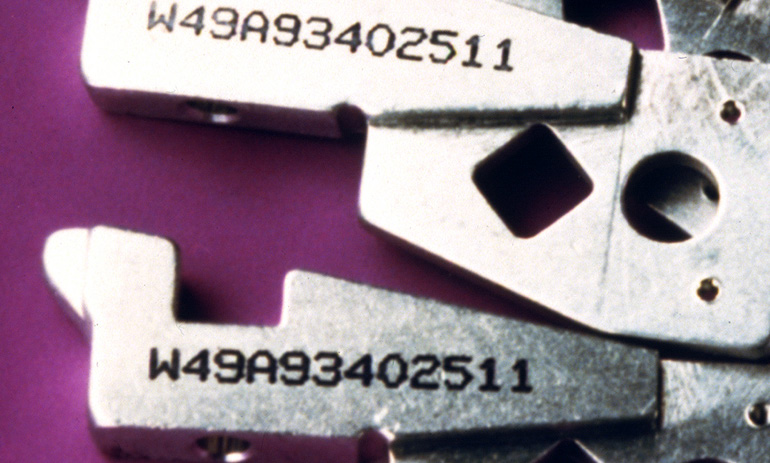
Solvent/chemical resistant; heat-cured
Many automotive and aerospace parts are exposed to environmental solvents such as oil, lubricants, antifreeze, and fuel. When cured at high temperatures (around 175°C/350°F for 30 minutes), codes printed with Videojet solvent/ chemical-resistant inks become resistant to offsetting or transfer and removal by steam, general abrasion, and many solvents.